If you play any part in the wiring of aircraft — whether as a manufacturer, installer or technician — then the acronym EWIS matters to you. The reason: EWIS stands for ‘Electrical Wiring InterConnect System’ or ‘Electrical Wiring InterConnection System.’ In either usage, EWIS represents a unified approach to aircraft wiring design and layout that encompasses all wires and wired devices that are installed in aircraft for transmitting electrical energy.
EWIS embraces “the wiring throughout the aircraft and its interaction with other systems,” observed Christopher Wollbrink. He is an engineer at Lectromec, which specializes in aircraft wiring system testing, assessment and certification. Its ISO 17025:2017 accredited lab is capable of doing most of the EWIS testing needed to verify component airworthiness, perform system-level tests, and determine long-term component reliability of aircraft wiring systems.
Christopher
Wollbrink
Lectromec
Why EWIS?
The impetus for developing EWIS as an overarching, unified approach to aircraft wiring and certification came from the 1996 TWA flight explosion of a Boeing 747 and the 1998 fire aboard Swissair flight 111 on a McDonnell Douglas MD-11, both of which resulted in the losses of the aircraft, passengers and crew. The rules governing EWIS are codified in the FAA’s Federal Aviation Regulations (FAR) Part 25, Subpart H — “Certification of Electrical Wiring Interconnection Systems on Transport Category Airplanes” — which were issued on December 4, 2007.
According to the National Transportation Safety Board’s official investigation report, “the probable cause of the TWA flight 800 accident was an explosion of the center wing fuel tank (CWT), resulting from ignition of the flammable fuel/air mixture in the tank. The source of ignition energy for the explosion could not be determined with certainty, but, of the sources evaluated by the investigation, the most likely was a short circuit outside of the CWT that allowed excessive voltage to enter it through electrical wiring associated with the fuel quantity indication system.”
Meanwhile, the Transportation Safety Board of Canada determined that the Swissair flight 111 fire “most likely started from a wire arcing event … A segment of in-flight entertainment network (IFEN) power supply unit cable exhibited a region of resolidified copper on one wire that was caused by an arcing event. This resolidified copper was determined to be located near manufacturing station 383, in the area where the fire most likely originated.”
Prior to these tragedies, aircraft wiring wasn’t seen as a potential source of serious in-flight incidents, which led to it being under-prioritized in comparison to avionics and other complex aircraft components and systems. Today, the EWIS approach ensures that wiring gets its due.
The Importance of EWIS
In a physical sense, EWIS is the central nervous system of an aircraft. It conveys information about
altitude, attitude, flight speed, and many other data points from sensor equipment to pilots. EWIS also allows them to fly the aircraft by conveying their commands to engines, rudders, ailerons and elevators.
An EWIS whose wires have degraded over time may not be able to function safely. This is why Lectromec performs degradation analysis testing on aircraft EWIS components and systems to identify current EWIS conditions and predict their remaining reliable service lives for up to 20 years.
“Wire failure effects are examined analytically, through simulation and, when necessary, through testing,” said Wollbrink. “This is done to generate data that EWIS engineers need for physical separation and verification of EWIS to aircraft component separation. We have an on-staff FAA DER (Designated Engineering Representative) and have worked on several aircraft certifications and STC projects performing wiring system testing and analysis.”
“The advent of EWIS as a maintenance approach has really highlighted wire material failures more accurately,” said J. Grant Lawton, an application engineer at W.L. Gore & Associates (Gore). It is a material science company specializing mostly in fluoropolymer and polytetrafluoroethylene products used in EWIS assemblies, cables and wires. “Before the EWIS approach came along, there was not a maintenance code for what actually happened to wires,” he said. “The codes typically used were related to connectors, contacts or other hardware and not the wire or cable when it was actually the problem.”
A case in point: in the pre-EWIS days, polyimide-insulated wire was widely used in aircraft. Unfortunately, polyimide wires tend to degrade in humid environments, to the extent that “the failure was so vast and widespread it could not be missed,” Lawton said.
According to a Lectromec white paper entitled, “Should Polyimide Insulated Wire be Trusted”, “In the early ‘90s, the threat posed by polyimide was well-established and began to become a feared wire for use on aircraft. This is reflected in the ban the Navy placed on installing polyimide wire for new aircraft applications in 1992.”
“With these defective materials identified, the entire industry worked over years to remove and replace all the polyimide insulated wire and cable,” said Lawton. “Had EWIS been in place, the problem would have been identified far sooner.”

W.L. Gore specializes in fluoropolymer and polytetrafluoroethylene products used in EWIS assemblies, cables and wires. W.L. Gore image.
Trends in EWIS Design
Aviation technology is undergoing major changes due to technological progress in materials and aircraft design, the ongoing miniaturization of electronics, and the increased collection of sensor data for preventative maintenance and more autonomous flight operations, among others.
EWIS design is part of this change process, as manufacturers tailor these systems to meet the trends shaping aviation in general. TE Connectivity manufactures advanced wire and connectors for aircraft EWIS, as well as the tubing and sleeving that connects them.
According to Matthew McAlonis, engineering fellow, aerospace at TE Connectivity (TE), there are two main trends that are driving the development of EWIS.
The first of this is the passenger experience. “Today, passengers expect comfort and uninterrupted and seamless connectivity to internet, social media and in-flight entertainment,” said McAlonis. “For example, connecting passengers requires building aircraft with ‘back-end’ systems that support wired and wireless interfaces so passengers can use their own devices, regardless of operating system. They also must support higher bandwidth, requiring use of high-speed cables and wiring, including fiber optic cables that enable long-distance gigahertz speeds to enable content such as streaming video.”
The second trend affecting EWIS design is the development of electric vertical takeoff and landing (eVTOL) aircraft, many of which are being developed for ‘air taxi’ applications. “Designing practical urban-air/advanced-air mobility (UAM/AAM) air taxis or electric-powered vertical-takeoff-and-landing (eVTOL) vehicles poses a new and complex set of challenges,” McAlonis continued. “Wire and cabling for these vehicles will require additional testing for mass proliferation. At TE, we are innovating on existing technologies through shape and weight optimization of components and cable assemblies.”
“There is a trend for ‘More Electric Aircraft’ which generally seeks to shift power, control and sensor systems to electrical power, and signal means in place of hydraulic, pneumatic or mechanical power transmission is expanding the use of wire and cable on aircraft,” Lawton agreed. But this is just one aspect of the electrical revolution that is driving EWIS design. For instance, “new technologies in controls, navigation, communications, entertainment and cockpit displays come with the need for high-speed data interconnects,” he said. “Vision systems, situational awareness, glass cockpits and better radars all bring new challenges needing better data cables — and since there are many more cables there is sensitivity to size and weight.”

Wiring manufacturers like TE Connectivity say their products can help provide passengers with uninterrupted, seamless connectivity to internet, social media and in-flight entertainment. TE Connectivity images.
Lectromec’s Wollbrink also sees the demand for high-speed data as influencing EWIS design. The challenge: “The need for higher speed data transfers requires tighter controls on product, fabrication and installation,” he said. “Cables need to be lightweight and robust to handle the stresses of being on an aircraft. Cables will also need to shield from unwanted signals from other devices to maintain signal integrity.”
The fact that eVTOLs will need high voltage (HV) systems to transfer power from their batteries to their electric motors is also affecting EWIS design. “With all-electric aircraft (AEA), the propulsion systems are running on voltages two-three times what we have historically seen on aircraft,” said Wollbrink. “It does not sound like much, but the industry wants the same package, weight, and longevity of these HV components as existing lower voltage systems. This has created a need for new designs, new materials and new ways to test and verify components.”
Challenges for EWIS Manufacturers
Collectively, the trends outlined above pose many challenges to EWIS manufacturers, as do customer requests in other areas. Here’s what they’re up against.
For TE Connectivity, many of their EWIS challenges are nothing new. For example, “customers are always looking for lightweight, toughened wire and cable constructions that offer improved resistance to chaffing and other forms of insulation damage, yet still meet the mechanical and electrical performance of wire and cable constructions that have been used by industry over many decades,” said Robert Moore, senior principal engineer at TE Connectivity.
As well, new EWIS products and materials always require certification in design, manufacturing, testing and application/use. “While industry demands have created an appetite for innovation, due diligence with the proper evaluation, testing and approvals cannot be ignored,” Moore continued.
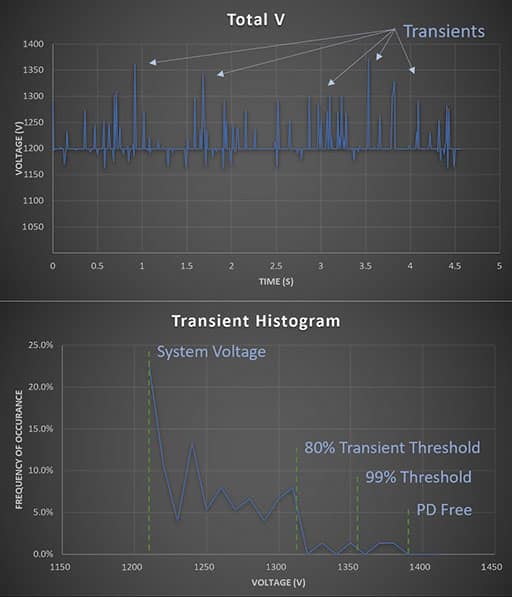
Lectromec 1: This image is from an analysis of voltage transients for a high voltage system and the performance level of the EWIS components. Lectromec image.
To move things along, TE engineers participate on standards committees supporting the aerospace industry, to get EWIS products with improved properties included in these specifications and approved for future platforms. “One example is the abrasion resistant XL-EFTE jacket used on our 55OTE family of cables that is now included in NEMA WC27500 as a jacket option,” said Moore.

Lectromec 2: Lectromec says finding new ways of testing and verifying their products is crucial. Shown here is a lab ASM D2671 flame test of heat shrink tubing. Lectromec image.
Gore’s solution to ever-evolving EWIS market demands is to produce wire and cables that offer multiple attributes, so there is less need for a ‘special’ high performance version, a ‘special’ small size version, and yet another ‘special’ lightweight version. “Gore has also used EWIS information from a specific platform to design a high abrasion-resistant wire product to help improve aircraft availability and reduce maintenance costs,” Lawton said. “That effort is improving wire and cable for the entire industry.”
Over at Lectromec, the development of eVTOL systems is motivating the company to put “extra effort into our lab development for HV systems,” said Wollbrink. To meet this demand, Lectromec’s lab has been upgraded using new technologies and assessment capabilities.
At the same time, Lectromec’s team has been performing research to expand their knowledge base. “With the push for aircraft electronics and HV systems, we have had to increase our power capacity, increase our capabilities around partial discharge assessment, and have a fuller understanding of the new power systems that impact the EWIS, and failure modes like electrical arcing faults,” Wollbrink said.
The Struggle to Get New Products to Market
Developing, certifying and getting new EWIS products is particularly challenging in the current high-pressure market environment. “New materials need to be tested and qualified,” Moore said. “Acceptance by an OEM then leads to that OEM sponsoring slash sheets into existing specifications referenced/used by the aerospace industry and qualification by TE to those documents.”

Robert Moore, TE Connectivity
“On the connector side, it is developing backshell accessories that make shield terminations during harnessing simpler and provide methodologies for improving EMI performance,” TE’s McAlonis said. All this has to be achieved while qualified personnel are in short supply: “In terms of talent, the industry needs more material science engineers that can evaluate and recommend new materials, and create proprietary formulations that can be evaluated by development engineering on products, such as wire and cable, heat shrinkable tubing, and P-clamp bushings, which are used in the aerospace market,” he continued. “Lastly, while the supply chain picture is improving, the lingering effects of shortages in commodity metals and resin materials has had an impact on manufacturing and time to market.”
Gore is facing challenges within the wiring ecosystem in creating new categories of industry specifications for next generation high performance cable. “Navigating standards for wire and cable products requires attention to detail and collaboration with customers and competitors to agree on effective and fair requirements,” said Lawton. “With that said, standards organizations such as SAE, EIA, ARINC and governmental agencies like NavAir, AFRL and FAA have a highly cooperative spirit that depends on voluntary participation.”
In contrast to the statements above, Lectromec does not have “any specific challenges with getting our products to market,” Wollbrink said. “We have been fortunate to be a voice of wiring system technologies for the last 40 years and as such, we are finding that a lot of the market is coming to us seeking our test capabilities and our experience for their platforms.”
Looking Ahead
To wrap up this look at EWIS trends and challenges, ATR magazine asked our experts what new products their companies are bringing to market now, and what they have planned for the future.
When it comes to new EWIS products, “one of TE’s most recent advancements is our lighter-weight, faster-to-install composite P-Clamps that mechanically bracket together wires, cables, or hoses and then fastens them securely to an anchor point — such as a screw or a bolt,” said McAlonis. According to him, the TE P-Clamp lock and mounting features give engineers more flexibility in configuring electrical and fluid systems. “The new design can significantly reduce installation time, up to 80% per clamp depending on the size, and potentially save hundreds of hours per aircraft build,” he stated. “Plus, the new P-Clamp reduces injury from repetitive motion, which can alleviate the physical difficulties of installing legacy-style metal P-Clamps.”
In fact, no tools are required for TE’s new P-Clamps, which are made of lightweight, aerospace-grade polyetheretherketone (PEEK) polymer. TE P-Clamps are available in 10 sizes, covering the same application range as standard AS21919 P-Clamps.
At W.L. Gore & Associates, their eyes are firmly on the future of EWIS. In this data-driven age, “system health monitoring will allow the aircraft to diagnose physical and electrical health in real time,” said Lawton. “From a wire and cable perspective, better quality materials and quality manufacturing will improve reliability on the front end.” As well, the adoption of data-based systems needing more and more bandwidth “are leading to different failure modes that we would call ‘Electro-Dynamic’,” he said, “meaning signal failure can happen at higher frequencies that would not be seen at low frequency or DC conditions. These are trickier to diagnose and require the EWIS to be evaluated in the frequency domain to ensure the cable connector and components are all working in ‘spec’.”
As for Lectromec? Looking forward, Wollbrink predicts that the major advances in EWIS technology will be in HV components and protection. “The wire and cable technologies of yesteryear are insufficient for high-voltage systems,” he said.
The technologies and lessons learned from other industries with high-voltage systems have played a role in the development of new wiring system technologies for aircraft, noted Wollbrink. Much of the knowledge in this area has been developed by the electric car sector. “Unfortunately, this also means that many of the technologies being implemented in aircraft are automotive-grade components,” he said. “This level of component reliability is insufficient for the requirements of the aerospace sector.” As a result, this sector will have to build on that work to develop EWIS and electrical power sources optimized for aviation.
This all being said, the future looks bright for EWIS development and improvements.
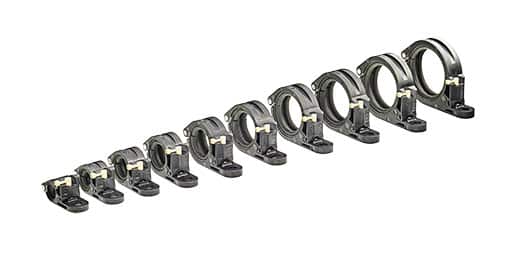
TE Connectivity offers a family of
P-clamps that are lightweight and
durable. TE Connectivity image.
“We are at the beginning of an exciting recovery in commercial air, where we see tremendous opportunities to further innovate with customers in in-flight entertainment, power and propulsion, and flight control in avionics,” offered McAlonis. “We are also on the cusp of fundamental change in air travel over the coming decade. With an increasing focus on sustainability, the aviation innovators of today are responding with design engineering advances that aim for zero carbon goals. We look forward to collaborating with pioneers and established players in the industry and aligning product roadmaps for high voltage, high speed, thermal management, and rugged fiber optics.”
You must be logged in to post a comment.